Tote Box Guide Info
Before you buy a tote box-any tote box-it will pay you to spend a few minutes in a simple analysis of your needs. We have devoted these pages to helping you to make this analysis. We hope that it will enable you to get the most for your material handling dollar.
What is a tote box?
Functionally, a tote box is a container which facilitates handling, storage, and processing of products and supplies. A single box may perform all three functions during a span of a few minutes; for now, however, let’s consider them separately.
HANDLING
Products, including parts and sub-assemblies, must often be moved prior to shipping as finished goods. This movement may be between storage areas and assembly areas, or from a production area to a shipping area. It may be a few feet, or interplant over many miles. It may be by hand, cart, conveyor, lift truck, or semi. In each case, the hand load is usually the basic module.
An efficient hand load consists of as much weight or bulk as one person can carry with safety. Few parts or products constitute an efficient hand load, in and of themselves. A tote box of a size and configuration to combine the largest practical number of parts into one hand load unit is the most practical method of handling parts and assemblies.
STORAGE
There are three important considerations when ordering containers for parts and product storage purposes.
1. Protection of contents: The container acting as a barrier against damage should include a cover to prevent contamination from dirt and moisture. It should be indestructible enough to withstand contact with other containers or objects stored next to or on top of one another.
1. Protection of contents: The container acting as a barrier against damage should include a cover to prevent contamination from dirt and moisture. It should be indestructible enough to withstand contact with other containers or objects stored next to or on top of one another.
2. Efficient use of space: The size and shape of the container should be considered as it best fits the storage area, whether it be racks
or shelving, whether you plan to store the containers separately or stack them.
or shelving, whether you plan to store the containers separately or stack them.
3. Ease of identification: To facilitate storage inventory control, the container you use should be labeled and, if possible, have see-through covers so quantity and contents type can easily be determined.
PROCESSING
Ideally, component parts should be transferred into tote boxes in the receiving department, at the very beginning of the process cycle. As the parts are incorporated into sub-assemblies, they again can be housed in tote boxes and moved through the system until the finished product is ready to be packaged for shipping. In some cases the tote box can be used for shipping purposes.
Other considerations include availability of space for containers at work stations and handling of contents for safe and efficient assembly and processing. Size of container will vary according to whether the operator is standing or sitting, by the variety of components to be assembled, and by the volume of parts required to maintain desired production rate. A wide variety of parts often calls for a variety of small containers at an assembly station. Alternatively, compartmented or kitted boxes, which will accommodate a mixed supply of parts for final assembly, can be used. In choosing the best container avoid boxes with sharp corners, or those made of materials which might chip or splinter. to eliminate the possibility of damage or contamination to delicate parts.
ECONOMIC CONSIDERATIONS
The “cost per use” is the key consideration in the selection of a container or tote box. Paying 25 cents for a paperboard box, using it once, and throwing it away, may be false economy compared to purchasing a box for $2.80 which may be used 100 times or more.
The cost of a box includes, in addition to base price, cost of acquisition, projected costs of maintenance during its useful life (e.g. cleaning and painting), and cost of disposal. Environmental problems associated with disposal are becoming more involved and more costly every day.
The “use” of a container depends on its function. In storage, “use” can be determined by time and environment; in handling or processing, “use” can be measured by the number of production cycles involved. In either case, the obsolescence factor must be considered; an expensive, custom box closely tailored to current requirements may have a shorter life than a more versatile, and perhaps less expensive box.
Other “hidden cost” factors to consider include possible damage to contents as a result of container-caused hostile environment (e.g. rust, paint chips, splinters, cardboard chaff, moisture, dust, etc).
COST COMPARISON
For the sake of an example, let’s compare the “cost per use” of two typical containers. Applying all the factors listed below to the “use” situation, we can compare the “use” cost of a paperboard container with a thermoplastic container as follows:
In this example, it is notable that the total “cost per use” of a thermoplastic tote box, that you can recycle/ is less than half of just the /’hidden cost” of a disposable paperboard box alone. This is not uncommon. Many users have replaced /’free/’ boxes (shipping cartons from suppliers) with thermoplastic containers and achieved demonstrable savings.
One more word about costs: even a medium sized manufacturing operation can utilize thousands of tote boxes, once they become established as a handling module. Since uniformity is usually beneficial, most users tend to standardize on the first type of box purchased. Therefore, the first purchase is very important. Not only must you establish which box or system will be most efficient, you must also guard against making a box material decision based on price alone. An arbitrary decision could result in thousands of dollars in extra costs due to an unfavorable “use” factor.
a) $30.00 per requisition and purchase order; purchased in 1M lots
b) l000, crushed but not compacted, will occupy approximately 2/3 of refuse container which costs $30.00 per pickup, or 02/box Equal amount to get box from point of discard to container
c) Crushed to greater bulk than paperboard
d) Failure rate est 1:l000: cost per failure, in terms of damage and cleanup, est $20.00 e) 25 production cycles per year for 3 years
|
MATERIALS
Tote boxes are made from many different kinds of materials, each having advantages and disadvantages as follows:
Paperboard: Inexpensive, most suitable for slow turnover storage applications because of low initial cost. Wears quickly with resultant contamination problems from chaff. Does not withstand effects of acid. Deteriorates when exposed to oil or moisture.
Metal: Rigidity and strength offer extended life advantages. More expensive than paperboard, dents easily. If painted, boxes tend to chip, can rust, and create contamination problems. Sharp edges may be a hazard Weight of larger containers may restrict “hand load” capacity
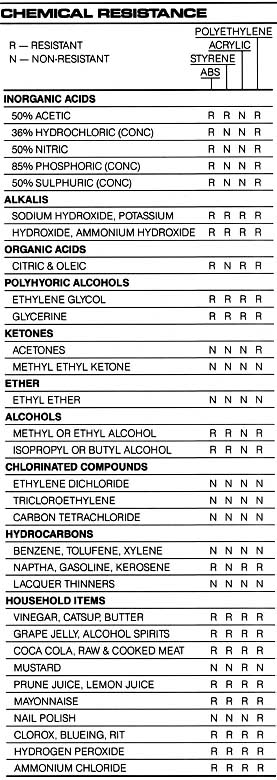
Wood: Major advantages: easy to fabricate “in house” for specialized uses. Strong and rigid. Expensive to fabricate, highly absorbent without protective finish. Splinters present hazard to workers, can contaminate parts. Pressed and impregnated fiber: Good for many light to moderate-duty storage and handling functions due to low initial cost and maintenance. Moisture and oil resistance, while much better than paperboard, is rarely sufficient for extended exposure. Generally low impact strength, subject to particulation and failure in rough use. Usually unsuitable for in-process parts handling due to rough and/or sharp surfaces.
Thermoplastics: As in other categories, quality can vary widely depending on what type of material is used. Thermoplastics range in cost from pennies to several dollars a pound. They are light-weight, moisture resistant, non-particulating, and require no maintenance. By type, styrene, polyethylene, polypropylene, and ABS are most commonly used.
Styrene: Relatively brittle, inexpensive and rigid. The best application is for very small transparent boxes where little abuse is anticipated.
Polyethylene: Especially high density, offers a good combination of qualities for most handling purposes. It is highly resistant to moisture, oil, most solvents and acids. Is extremely tough, light-weight and economical. Because of its low-friction surface, it is usually unsuitable for use on conveyors, especially where there are inclines. Its propensity to hold a static charge may tend to attract dust. Low creep resistance and low dimensional stability may limit use for very heavy loads. Translucency and tooling marks may create objectionable appearance.
Polypropylene: Similar to polyethylene, does not have the surface toughness to resist abrasion. High temperature and solvent resistance make it the choice in many situations.
ABS (Acrylonitrile-Butadiene-Styrene):
Material used for telephones, is tough, relatively rigid and offers good acid and solvent resistance. Appearance and dimensional stability are good. Easily fabricated. An engineering thermoplastic, it is somewhat more expensive than others mentioned above.
Material used for telephones, is tough, relatively rigid and offers good acid and solvent resistance. Appearance and dimensional stability are good. Easily fabricated. An engineering thermoplastic, it is somewhat more expensive than others mentioned above.
STATIC CONTROL MATERIALS
Virtually all PCC products are now available in conductive or static dissipative materials. Please see “Static Control Products” section for applications and specifications.
PCC Tote Boxes can be utilized in many phases of your operation, enabling you to realize cost savings, increased efficiency and faster production.
1. RECEIVING/INSPECTION
PCC Tote Boxes help organize assembly parts in receiving department for original check. These handy containers protect component parts as they move from station to station, increasing production efficiency and saving space. They eliminate the need for in-process protective packaging. . .cut handling and protective material costs. . . and eliminate the problem of disposing of these protective materials.
2. MACHINING
In the manufacturing process, internally produced or machined parts are organized in PCC Tote Boxes which efficiently protect critical surfaces as they are transferred to finishing, and assembly operations.
3. STORAGE OF FINISHED PARTS and SUB-ASSEMBLIES
Using PCC “stacking type” boxes. with stacking lugs, loaded boxes can be stacked in any desired multiples with positive clearance for contents. For materials which require extra protection from dust and damage, “standard type” boxes can be used with clear plastic or ABS covers which make high tiering possible without danger to contents.
4. ASSEMBLY
Tote Boxes carry sub-assembly components to assembly points. Different components can be separated, protected and made quickly available for final assembly when stored in PCC Tote Boxes. Compact, lightweight, they are efficient work organizers.
5. OUT-PLANT OPERATIONS
PCC’s Tote Boxes provide the ruggedness and durability necessary for greater protection and safer handling of products for out-plant transportation, as well as in-plant movement and storage.
6. IN-PROCESS INVENTORY STORAGE
Finished parts and sub-assemblies can be stored for immediate or future use as needed. Color coded or end labeled for easy identification, PCC Tote Boxes provide the answer to constant inventory control. Clear covers permit quick confirmation of contents. Modular sizes assure maximum use of standard racks, carts and shelving.
7. CLEAN ROOM INSPECTION and ASSEMBLY
PCC Tote Boxes are excellent clean room tools. They protect vital parts from dust, dirt, moisture and foreign matter. Smooth interior surfaces without sharp corners or crevices permit easy cleaning to comply with military specifications. They do not accumulate dust or dirt so damaging to delicate parts.
8. FINAL INSPECTION
Damage and handling costs are greatly reduced in final inspection where finished product is taken from PCC Tote Box, checked and replaced in the box for finished goods inventory or transfer to final packaging and shipping operations. PCC Tote Boxes may be used as returnable shipping containers. Their multiple sizes, shapes and dividers insure safe transit. Flexibility of PCC Tote Boxes can be increased by changing compartment sizes with “egg crate” dividers which fit all standard models.
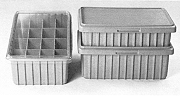
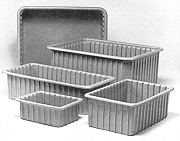
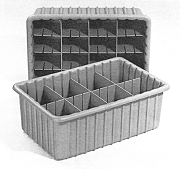